Quality & Compliance
Exceed compliance standards to drive solutions that support better outcomes.
.png)
.png)
-4.png?width=650&height=425&name=Untitled%20design%20(6)-4.png)
An industry leader in quality & compliance
At ProPharma, our expansive team of consultants and subject matter experts support a diverse spectrum of products, including drugs, biologics, medical devices, and diagnostics. Our dedicated team of experts specializes in providing comprehensive solutions tailored to the unique technical and quality requirements of each product category. Whether you are embarking on the development journey for your first drug or biologic, or you are an established company in the device and diagnostics sector, we have the expertise to guide you through the complexities of ensuring product integrity and reliability.
The development paths for drugs, biologics, medical devices, and diagnostics vary significantly, each presenting its own set of technical challenges and quality considerations. At ProPharma, we understand the critical importance of maintaining rigorous quality standards and ensuring GxP compliance throughout the product lifecycle. With our expertise in quality assurance, validation, and regulatory compliance, we can assist you in navigating the intricate technical landscape with confidence. By partnering with ProPharma, you can be assured that your products will meet and exceed the highest standards of quality and regulatory compliance from development through to commercialization.
Quality & Compliance Services
An expansive suite of services to ensure quality, compliance, efficiency, and safety throughout the full lifecycle of a product. Our Quality & Compliance experts support you with the highest quality of services by providing best practices and proven insights on program and process management.
Consulting Services
ProPharma's Quality and Compliance Team offers consulting services to assist clients in navigating the complexities of GxP compliance. Our dedicated experts provide guidance to help you make informed decisions about the regulatory challenges you face. Whether you have questions regarding Good Manufacturing Practice (GMP), Good Clinical Practice (GCP), Good Laboratory Practice (GLP), or other GxP standards, we will connect you with an industry expert equipped to address your specific needs. With extensive experience across almost every facet of healthcare, our team has completed thousands of projects, delivering compliant and effective solutions in an efficient manner. You can count on ProPharma to provide the expertise and support you need to achieve and maintain GxP compliance throughout your operations.
Computer System Validation
ProPharma's validation professionals leverage the latest risk-based Computer System Validation (CSV) and Computer Software Assurance (CSA) techniques to ensure that our clients' systems are ready for inspections from the FDA, EMA, MHRA, and other regulatory agencies. Our consultants have extensive experience in the pharmaceutical, biotech, medical device, clinical research, and software industries.
- Cloud-based (SaaS and PaaS) applications
- Configured Off-the-Shelf (COTS) applications
- On prem and cloud-based (IaaS) infrastructure
- Initial validation, retrospective validation, and ongoing validation for software updates
Part 11 and Annex 11 Compliance
Compliance with FDA 21 CFR 11 Electronic Records; Electronic Signatures and EU Annex II Computerised Systems is a must in our industry. If your organization's growth depends on compliance with Part 11 or Annex 11, ProPharma has the experts you need to get your systems, procedures, validation documents, and employees ready.
Data Integrity
Data without integrity puts patients at risk. Data Integrity is a "hot topic" because many of the controls implemented decades ago for paper records, have not yet been implemented for electronic records and computer systems in spite of recent guidelines from the FDA, EMA, MHRA, PIC/S, and WHO. Our experts have experience applying the ALCOA principles to real-life scenarios to minimize data integrity risks through remediation of systems, policies, procedures, and data governance programs.
GxP Compliance
ProPharma specializes in solving complex challenges. Our experienced compliance consulting professionals will seamlessly integrate with your team to do more than simply identify potential risks. We provide recommendations to mitigate those risks and will work side-by-side with you to implement improvement plans and collaborate with your team in addressing those risks.
From early concept development through each clinical phase, product launch, and commercialization, our Quality and Compliance Consultants partner with clients around the world to help ensure regulatory expectations are met, such as compliance with DSCSA and EU FMD, business goals are achieved, and patient health and safety is assured and improved. We do this with an unwavering focus on delivering the highest quality services through our diverse team of qualified subject matter experts (SMEs). Having working experiences from large international corporations to small research companies as well as authorities such as FDA, EMA, MHRA, and national competent authorities, our experts drive operational excellence and provide a sincere commitment to providing high-quality services. Our ability to be nimble coupled with a passion for excellence ensures our consulting services exceed clients’ expectations.
ProPharma performs quality and compliance consulting activities in all GxP areas. Our consultants have extensive management and operational experience in at least one GxP area (GMP, GDP, GVP, GCP, GLP, GCLP, and/or IT/CSV) and often in multiple areas of expertise.
GxP Audits
Any firm that outsources regulated activities such as clinical studies, manufacturing of pharmaceutical products or medical devices, production of raw materials, or laboratory services requires routine qualification audits.
Companies are expected to be compliant and continuously improving. As your partner, we maintain alignment with new, existing, and changing regulations and industry standards that evolve throughout the drug product and device lifecycle. Our GxP auditors have real world experience supporting regulatory inspections and preparing companies for pre-approval inspections (PAI).
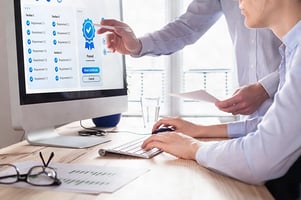
Our team of specialists includes former regulatory agency inspectors and qualified auditors who are proficient in conducting mock inspections, internal audits, vendor and supplier auditing, and gap assessments. We serve as an extension of our client’s Quality Department with respect to vendor and supplier auditing or act as a mock regulatory agency representative with respect to preparing your organization for an agency inspection. Partnering in a constructive and collaborative manner, we work together to understand, identify, and evaluate systems for quality improvements.
With offices and quality and compliance consultants located all over the world, ProPharma offers the availability to execute audits in different GxP areas on a global basis with diverse language skills, creating efficiencies in both time and money. Our large team of qualified auditors have a breadth of expertise across the entire development and regulatory spectrum (GMP, GCP, GLP, GCLP, GPV, ISO-13485, CSV, Data Integrity, etc.).
Quality Investigations and CAPA Support
A key component of any modern quality system is the risk-based response to observed manufacturing, testing, and distribution discrepancies, or as the result of product complaints. Good Manufacturing Practice (GMP) regulations and industry guidance all describe the criticality of implementing a structured approach to performing investigations with the intent of determining root cause of the discrepant issue. Determining the root cause is necessary to implement specific and effective corrective and preventative action (CAPA) to remediate and prevent reoccurrence of the issue, and consequently facilitate continuous improvement.
For over 20 years our experts have delivered thousands of investigation reports with teams ranging in size from a single investigator up to teams of 45+. Our project success follows a thorough project initiation procedure that dictates everything from onboarding to resource loading through execution of deliverables and metrics reporting. Our diverse and experienced SMEs are another key to our success. The lifecycle of discrepancy and complaint management can be quite complex and often requires input from multiple subject experts. ProPharma has all the experts needed to support your program. Our team will integrate with yours and provide investigation and CAPA support within your quality system, or we will help to develop and optimize your program. Our team has a wealth of knowledge accumulated through many years of industry support in consulting roles as well as operating company management defending investigation and CAPA systems to regulatory bodies.
When you partner with ProPharma, you gain the experience of the entire company—not just the team assigned to your project. This breadth and depth of knowledge enables ProPharma to provide you with the support and guidance you need when you need it.
EU and UK Batch Release through the ProPharma MIA License
Navigating both the specific country and general European regulations and requirements to supply medicinal products to the European markets can be a complex challenge. This applies both to Marketing Authorisation Holders (MAH) of approved medicinal products and sponsors of clinical trials.
On top of the varying requirements, MAH/Sponsors looking to enter the European markets must create tailored supply strategies per country and establish a legal entity with a Manufacturing and Importation Authorisation (MIA) and a named Qualified Person (QP) in the region.
All of which can be extremely difficult for even the most experienced individuals. The QP is responsible for ensuring that each individual batch has been manufactured and checked in compliance with laws in force in the Member State where certification takes place, in accordance with the requirements of the marketing or clinical trial authorisation (MA/CTA) and with GMP.
Partnering with the leading industry compliance experts will help unravel these complexities to improve business efficiency, shorten timelines, and reduce overall costs. This will allow you to further focus on product development, clinical studies, and commercialization to support patient access and safety.
ProPharma hold both EU and UK MIAs which allows us to help clients overcome the complexities of accessing the EU and UK markets, like navigating country and EU regulations and creating tailored strategies per country. It also negates the need for MAH/Sponsors to obtain its own MIA license with a QP in the region. All of which helps ensure products are released to patients in need across the EU and UK in a quick and flexible way. Especially if speed to market is an issue since obtaining an own MIA license is a much longer process (>1 year) compared to listing your medicinal products on ProPharma's license (3-4 months).
ProPharma can perform QP Batch Certification services under its own MIA licenses for pharmaceutical and biotech clients launching products to the European and UK markets, as well as release for export from the EU (e.g., to the United States). This applies to both new and existing products. Listing your products on the ProPharma MIA licenses gives you access to skilled and experienced QP's for multiple types of products/formulations including biologics, ATMPs, vaccines and small molecules.
Qualified Person (QP), Responsible Person/Responsible Person Import (RP/RPi)
Every organization in the life sciences industry is required to have a current and compliant quality system to ensure the safety and quality of all products and services. Quality assurance entails the maintenance of a desired level of quality in your products during every stage of the process, from production to delivery.
At ProPharma, our quality assurance professionals augment your internal capabilities to ensure products are consistent and safe. Our team acts as an extension of your Quality Unit, utilizing a hands-on and risk-based approach to quickly improve quality and compliance, and implement practical solutions for your organization.
Companies that intend to manufacture or import medicinal products in the EU and UK require an MIA license and a designated named Qualified Person to oversee the product quality throughout the supply chain. Acting as an extension of your organization, our QP consultants bring a deep understanding of GMP processes. They work with your team to ensure compliant manufacturing and/or importation of products in the EU and UK markets. Our global team of certified QPs have broad experience covering multiple types of formulations, complex supply chains, technical transfer projects, aseptic/sterile manufacturing, radiopharmaceuticals, biologics, ATMPs and supply for clinical trials.
WDA (Wholesale Distribution Authorisation) Licence
To procure, sell and distribute medicinal products in the EU/UK markets you need a Wholesaler Dealer Authorization (WDA) and a Responsible Person (RP) named on the license. A WDA in the UK can also be used to import QP-certified medicinal products from the EU. In that case you would need a Responsible Person (import). The RP has the quality oversight of the company's wholesale operation and has the main responsibility to assure compliance with GDP regulations and that the quality of the products distributed is maintained.
Our highly experienced RPs can act as contractors named on your, or a third party's, WDA for both human and veterinary medicines under EU and UK Guidelines. If you are new to the EU/UK market we can help you navigate the road from QMS build, through the WDA application process, a successful inspection and obtaining your very own WDA license.
Remediation
Whether you have small- or large-scale operations in pharmaceuticals, biotechnology, medical device, or compounding pharmacies, we offer risk-based remediation services that can benefit your organization.
ProPharma has a unique team of remediation professionals that organize and communicate the requirements of the remediation effort. This remediation team enables us to identify and track every action item required for compliance remediation and escalate potential concerns to project teams and/or executive management for resolution. We partner with you to build your remediation plan, perform gap assessments for all systems, and implement remediation efforts to ensure you are on schedule and within budget.
Regardless of your challenge, our team understands the complexities associated with compliance constraints and can support your organization to manage the remediation process to return your organization to an efficient and compliant operation.
Quality Management Systems (QMS) Development and Optimization
For pharmaceutical, biotech, and medical device manufacturers, Quality Management Systems (QMS) are the foundation for enabling the organization to operate in a compliant manner. The QMS establishes the path to compliance for the company and enables sustainable systems that meet the demands of regulators, customers, and ever-changing business environments.
We are a trusted partner in designing, building, and managing QMS programs. Our industry-leading experts understand the complex regulatory elements and the compliance systems that are required for your organization to succeed. We can help guide your team through the regulatory processes specific to your quality programs.
Our professionals ensure QMS achieves three objectives:
- Continuous improvement
- Regulatory requirements
- Establish “right-sized” processes for the phase and scope of the organization
Inspection Readiness
A key component of business continuity for a firm, whether in the business of pharmaceuticals, medical devices, biotech or beyond, is its ability to successfully navigate an inspection of any type, or beyond, is its ability to navigate an inspection of any type successfully. Firms are expected to maintain a level of compliance with the appropriate regulations or continuously optimize, and in some cases, remediate. As your partner, ProPharma's experience and expertise will help you do just that. Whether it is a For Cause Inspection, a Routine Inspection, a Pre-Approval Inspection (PAI), or Bioresearch Monitoring (BIMO) Inspection, our experts can guide you through this significant milestone. With extensive experience in all inspection types, and utilizing our tried and tested Inspection Readiness processes, your firm will successfully negotiate your upcoming inspections.
Program & Project Management
We understand that you are constantly faced with complex projects with tight timelines, finding or freeing up resources to meet those deadlines, and are often dealing with trying to balance your daily work with yet another urgent initiative or critical pipeline project.
ProPharma’s Project Management offering provides the right resource or solution for the right project at the right time. Our project managers have seamlessly joined teams and successfully implemented projects, pipeline programs, and other transformational initiatives within pharmaceutical, biotech, and medical devices and diagnostics companies. Our practitioners share a winning approach that blends insights from their subject matter expertise, prior project successes/lessons learned, peer learnings, and fit-to-purpose project design.
Project Area Expertise
- R&D Life Sciences Projects
- Early and Late-Stage Drug Development
- Pre-Approval Inspections (PAI) Readiness
- Product Development – Pharmaceutical, Biotechnology, Medical Device and Diagnostics
- Quality Assurance – R&D and Manufacturing
- See more about Program & Project Management
We Specialize in These Types of Challenges
- Identifying and staffing a skilled project manager to support your project needs
- Providing program management support for early- or late-stage drug development programs
- Providing project management support for pre-approval inspection readiness and regulatory filings
- Overseeing remediation efforts for device, diagnostic, or drug inspections and audits
- See more about Program & Project Management
R&D Process Optimization & Organizational Change Management (OCM)
We understand that throughout the R&D lifecycle, you are faced with multiple challenges such as addressing a process that is not efficient, looking for productivity opportunities, or developing a brand-new process. ProPharma’s process optimization approach is collaborative in that we work with you to understand and address your process challenges while using a methodology rooted in lean six sigma and other industry leading process optimization techniques. Our experts will help you optimize your processes at any point in the R&D and Commercialization lifecycle.
Post-Merger Integration
When your organization makes a significant investment in acquiring a new organization, excellence of post-merger integration execution is critical. But, for a Quality Assurance (QA) organization, there is an added complexity as both legacy organizations must execute ongoing activities and remain in compliance. Our methodology and expertise in executing these activities can complement or drive your integration activities so you can realize integration success.
Technology Transfer
We understand that as transfers of products and processes from one site to another are becoming more common, transfers can be complicated, lack detailed technology transfer plans, lack quality documentation, and/or lack internal expertise or have the bandwidth to efficiently complete the transfer.
We can effectively work with you using our proprietary and customizable Gated Technology Transfer methodology to meet your specific production and technology demands: development to production or from site to site in a compliant and efficient manner. We have successfully completed more than 175 product transfers using our Gated Technology Transfer approach. Clients credit this impactful methodology in helping them navigate the complexities of the technology transfer process while realizing efficiencies along the way.
Vendor Selection & Management Services
We understand that identifying and managing vendors can be overwhelming due to the sheer volume of options and the need to follow a structured and data driven path to make a decision.
Our identification services will save you time and effort by allowing us to interview you to understand your vendor needs, identify key selection criteria, and use our methodologies to identify potential partners. We have deep expertise in working with R&D and Manufacturing clients to manage the RFP process through the selection and confirmation processes to confirm the partner.
For management, we can work with you to develop and roll-out ongoing proactive governance and audit processes to ensure that your vendor’s objectives and activities are being completed as agreed upon contractually and there is a mechanism for issue and risk identification, escalation, and management.
Commissioning, Qualification and Validation
At ProPharma, our life science consulting experts provide process validation services for the design, qualification, and continued verification of manufacturing processes that help clients maintain quality and compliance for cGMP regulated products.
Our global teams partner with you to ensure that each step of the validation process is properly mapped and executed. By working with our process validation experts, you can deliver the documented evidence needed to guarantee to regulatory agencies that careful and systemic attention is applied and that your product meets the necessary quality attributes.
ProPharma's product lifecycle approach towards process validation in pharmaceuticals and biotech helps you deliver optimal product quality by identifying the presence and degree of process variation and the impact variation has on the process efficiency and product quality. Minimizing the variation reduces risks and ensures a robust process that reliably produces quality product.
Defining the commercial manufacturing process based on knowledge gained during development and scale-up activities.
Process Design
Defining the commercial manufacturing process based on knowledge gained during development and scale-up activities.
- Initial process design experiments do not necessarily need to conform to cGMP. This step should be based on the guidance of sound scientific foundations.
- It is essential to follow good documentation practices. The studies that show an improvement of process understanding should be documented.
- Repeated testing at this phase, until the process fails, is not generally expected according to the guidelines of the FDA.
- The creation of process controls are required to ensure product quality, and also cover any variability in product. The FDA requires process controls to cover the examination of materials and equipment monitoring. Process control and monitoring is essential under the following circumstances:
- The product attribute is not easily detected or measured
- When products/intermediates are not well characterized.
Process Qualification
Performing the necessary evaluations to determine if a process is capable of reproducible commercial manufacturing.
- Proper design of manufacturing facilities is necessary under cGMP requirements
- Choosing appropriate utility systems and equipment. Equipment and utilities should be chosen according to documented design specifications.
- Verify that systems and equipment will perform within the necessary specifications
- Process Performance Qualification (PPQ) should be conducted holistically with the qualified utilities, facilities, equipment, and trained personnel associated with the manufacturing process. When possible, the FDA prescribes that objective measures such as statistical metrics should be utilized.
- Written protocols and expected outcomes are crucial to process validation during this phase. Manufacturing conditions, sampling plans, required tests, and data collection are highly recommended to be included in protocol descriptions.
Process Verification
Developing ongoing monitoring during production to verify that the process remains in a state of control.
- cGMP guidelines recommend developing procedures to gather and evaluate data relevant to product quality.
- Following cGMP principles and industry best practices are essential when determining variability.
- FDA guidelines state that sampling and monitoring in this phase should continue at PPQ established levels until enough data are accumulated to make significant variability estimates.
- The maintenance of the utilities, facilities, and equipment is also important during this phase.
Cleaning and Sterilization Validation
All manufacturers, hospitals, pharmacies, and medical device manufacturers require cleaning and sterilization. We partner with organizations to develop and implement continuously reliable and compliant validation programs that help clients successfully bring products to market.
Our sterilization services include the physical (IQ and OQ) and microbiological inactivation (PQ) testing aspects for steam sterilization, dry heat, and vaporized hydrogen peroxide.
Our cleaning services involve a defined clustering approach of products, protocols, defined assays and limits, protocol writing, in-test lab selection support, execution of testing support, and reporting that result in effective controls for limiting the bioburden.
Good Manufacturing Practices Product Lifecycle Methods
ProPharma knows how to leverage regulatory agencies’ requirements to ensure each phase of your product manufacturing lifecycle is successful.
Our associates include pharmacists, chemists, engineers, and microbiologists, all with industry experience in various aspects of product environments. This experience ensures the analytical techniques used are robust, accurate, and reproducible throughout the product lifecycle. We apply industry knowledge and methodologies to ensure your products provide the expected accuracy and repeatability needed to safeguard them through the manufacturing lifecycle by:
- Evaluating the reliability of the product analytical methods
- Determining the methods perform as intended and are reproducible between laboratory and manufacturing sites
- Partnering with your organization to confirm every aspect of production occurs in a cGMP environment with the necessary controls in place, and evidence of those controls published
Medical Device
The path for medical devices and diagnostics trials is different from drug development, which is why we have a dedicated team of experts who focus solely on supporting our device and diagnostics clients. Our experts understand what it takes to get these products to market and help design efficient and compliant trials to help meet your goals.
We help our clients navigate the regulatory challenges in both the US and EU associated with devices and diagnostics.
Quality Systems
For medical device manufacturers and their third parties, Quality Management Systems (QMS) are the foundation for enabling the organizations to operate in a compliant manner and provide a strong foundation for business management. The QMS establishes the path to compliance for a company and enables sustainable systems that meet the demands of regulators, customers, and ever-changing business market environments.
We work with all sizes of companies to help design, implement, or remediate a QMS based on business needs and regulatory expectations. We can help guide your team through the regulatory processes specific to your product and provide comprehensive training for your company. We have experience with medical devices, diagnostics, combination product, companion diagnostics and Software as a Medical Device (SaMD). Our experts have industry experience and often prepare and support our clients throughout the audit and approval process.
Our professionals ensure any QMS achieves three objectives:
- It is appropriate for the phase of development of the product, type of product, and scope of the organization. Understanding your company’s business and resources, we develop a "right-sized" solution that ensures compliance while minimizing burden
- It establishes the foundation for regulatory compliance and continuous improvement
- It comprehends the regulatory requirements for all planned markets
Medical Device Remediation
With our extensive experience with ISO 13485, 21 CFR part 820, and other global regulatory requirements for medical devices and diagnostics, we can support your remediation activities across the entire product lifecycle. Our team supports both proactive remediation projects, like the transition to Medical Device Regulation (MDR) and In Vitro Diagnostics Regulation (IVDR), or reactive remediation projects, such as warning letters, 483s, or other deficiencies identified by other global regulatory bodies.
We routinely help clients across the product lifecycle navigate the regulatory frameworks around the world, providing risk management, design control, and technical documentation help to support their products in their target markets. Regardless of whether you need a quality expert to support your team as they work through quality issues or need help strengthening your team as they perform the incremental work to meet the ever-growing compliance expectations for medical devices and diagnostics, we can help.
Medical Devices and Diagnostics Program and Project Management Support
In addition to the traditional program and project management support, we have project managers that have worked extensively within the medical device and diagnostics areas and can help set up a project or program, provide project management resources to support a project or get an existing project back on track. We have deep expertise with clients of all sizes across the entire product lifecycle from early feasibility through design control, submission, launch and post market support; we can provide the project management support to meet the needs of each client.
We also offer an industry-leading, focused workshop utilizing a proven process successfully used over 250 times for medical devices and diagnostics clients. The process takes approximately three weeks to complete and results in a team aligned on the project objectives, a project charter, resource plan and timelines. This approach has been used, for example, to launch a new project or to realign an existing project that may have changed scope or is facing key challenges.
Healthcare Compliance Services
Staying compliant in today’s complex healthcare environment is essential for protecting patients, maintaining operational efficiency, and avoiding costly penalties. ProPharma’s healthcare compliance experts provide tailored solutions that reduce risk, support regulatory readiness, and streamline operations. From Joint Commission survey prep and pharmacy audits to site inspections and mock surveys, we help healthcare organizations stay audit-ready, safeguard reputation, and improve patient care quality.
Quality & Compliance Experts
-
Simona Mills
Director, Product Lifecycle Management
-
David Crome
Managing Director, Quality & Compliance UK & India
View Bio
-
Eric Good
Director, Compliance & Quality Assurance
-
Ben Frey
Vice President, Compliance & Quality Assurance
-
Deb Bartel
Vice President of Quality Assurance
Simona Mills
David Crome
With over 45 years of experience in the pharmaceutical industry, David Crome has worked with both branded and generic multinational companies, including a decade in consultancy. His career has spanned most functions in the industry, covering the entire product lifecycle: R&D, regulatory, production, QA, supply chain, auditing (with over 150 audits undertaken), marketing, setting up new businesses, and assisting clients in attaining EU/UK GMP certification. David has participated in over 60 regulatory inspections conducted by various agencies, such as the MHRA, HPRA, EMA, SUKL, USFDA, SAHPRA, and Anvisa, across England, Ireland, Argentina, Bangladesh, the Czech Republic, and India.
Eric Good
Ben Frey
Deb Bartel
News & Insights

April 18, 2025
Navigating FDA Layoffs: How Policy Layoffs May Impact Generic Drug Development
Explore how FDA layoffs affecting the OGDP may impact generic development & how experienced regulatory consultants can help you stay on track.
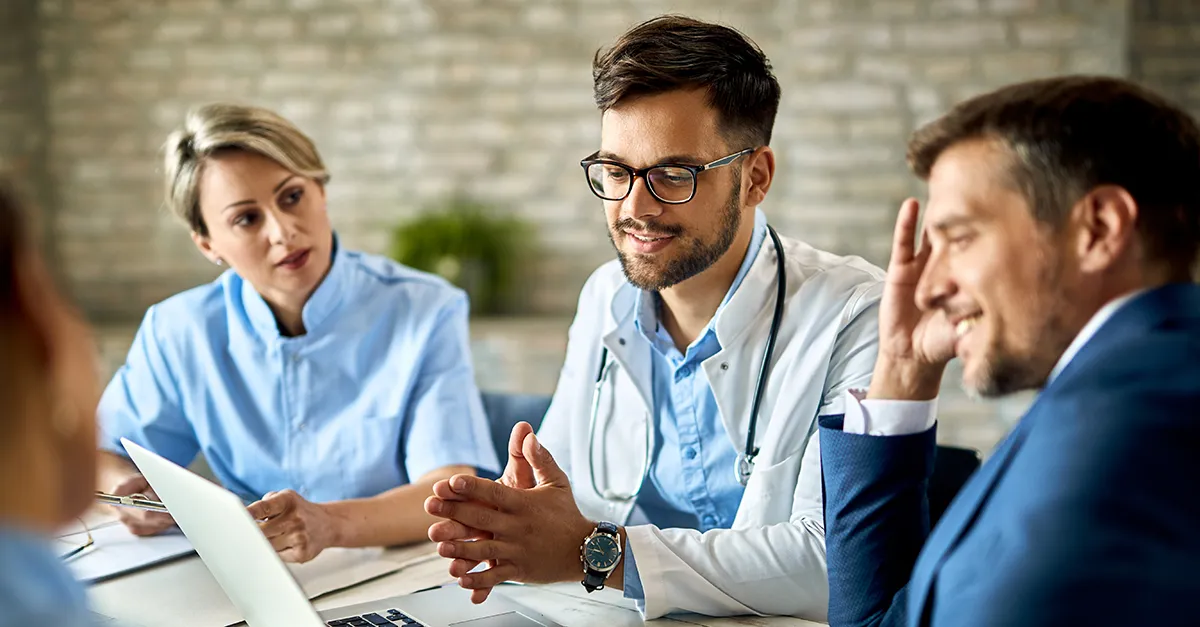
April 17, 2025
Navigating FDA Layoffs: OPDP Cuts and the Rising Stakes of Ad Compliance
Recent FDA layoffs within OPDP signal major shifts in drug ad oversight. Maintaining compliance is more critical than ever and regulatory experts can help mitigate any risks.
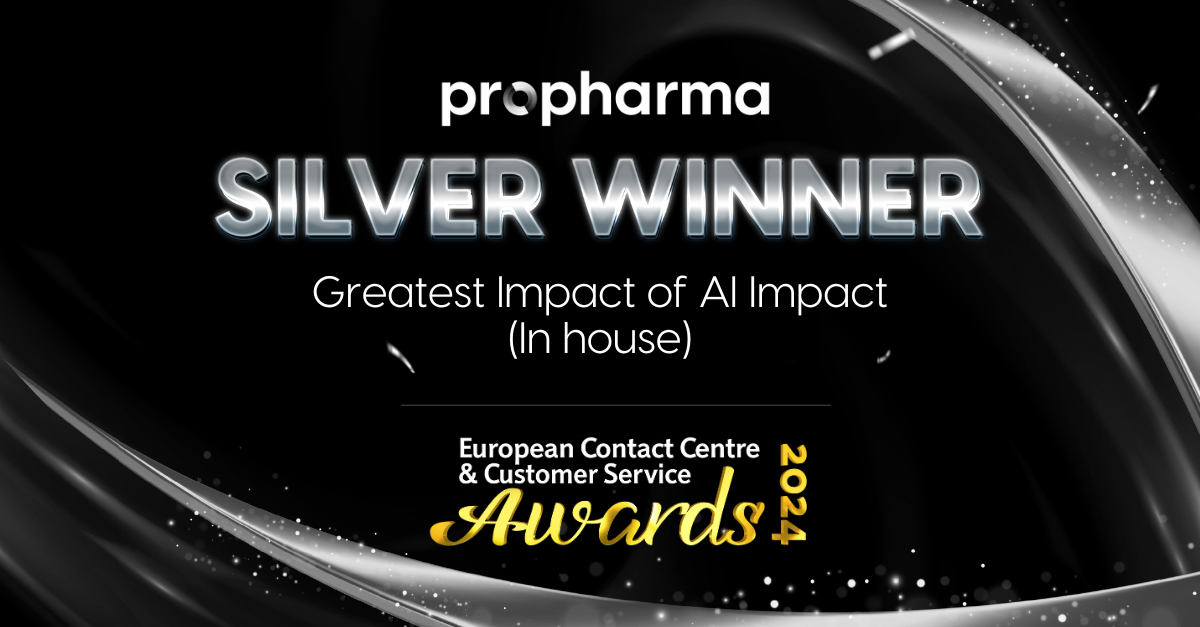
January 31, 2025
ProPharma Recognized for AI Excellence at ECCCSA
ProPharma wins Silver at ECCCSA for AI innovation in Medical Information, enhancing efficiency and quality in delivering accurate medical information.
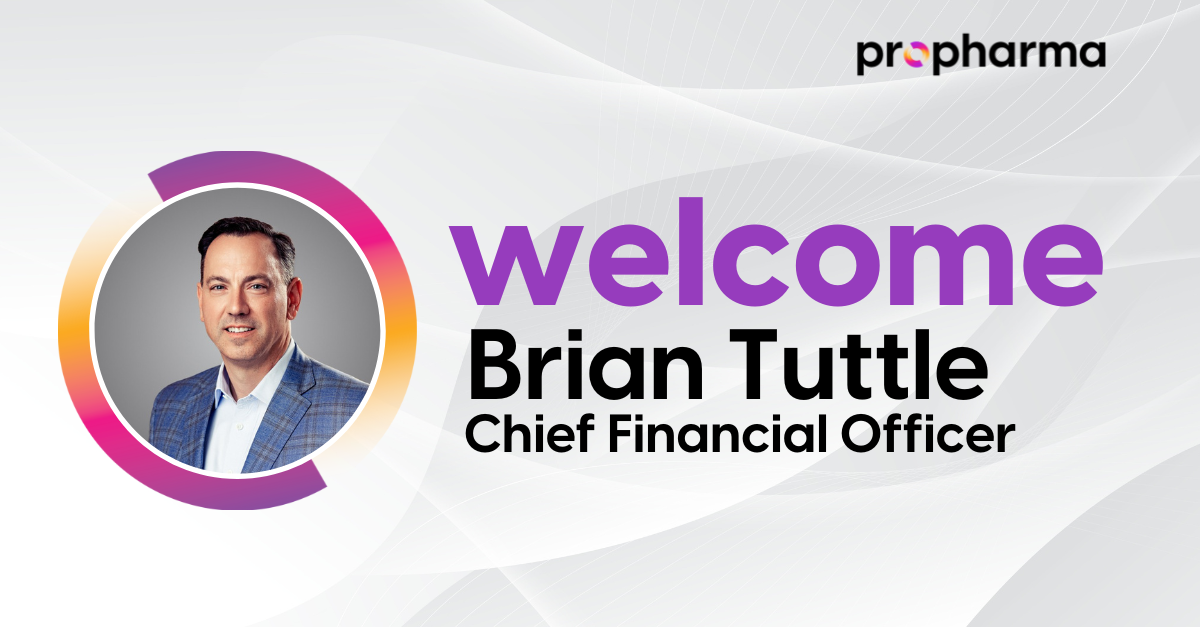
October 21, 2024
ProPharma Appoints Brian Tuttle as Chief Financial Officer
ProPharma appoints Brian Tuttle as CFO to drive financial strategy and accelerate global growth, leveraging his 20 years of life sciences industry experience.
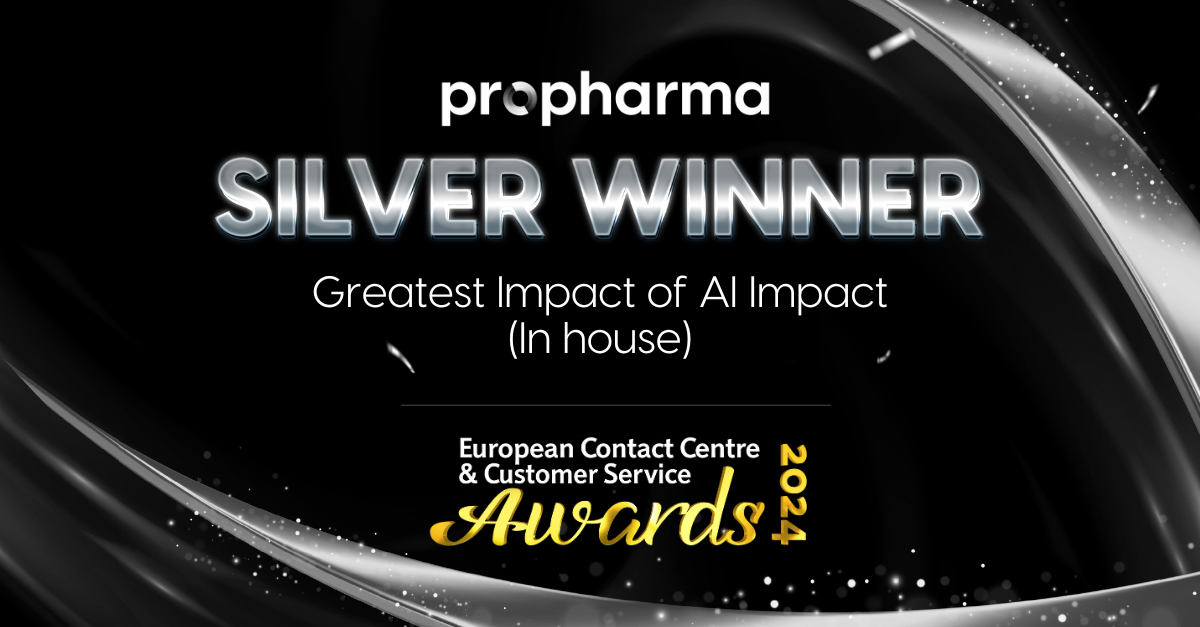
January 31, 2025
ProPharma Recognized for AI Excellence at ECCCSA
ProPharma wins Silver at ECCCSA for AI innovation in Medical Information, enhancing efficiency and quality in delivering accurate medical information.
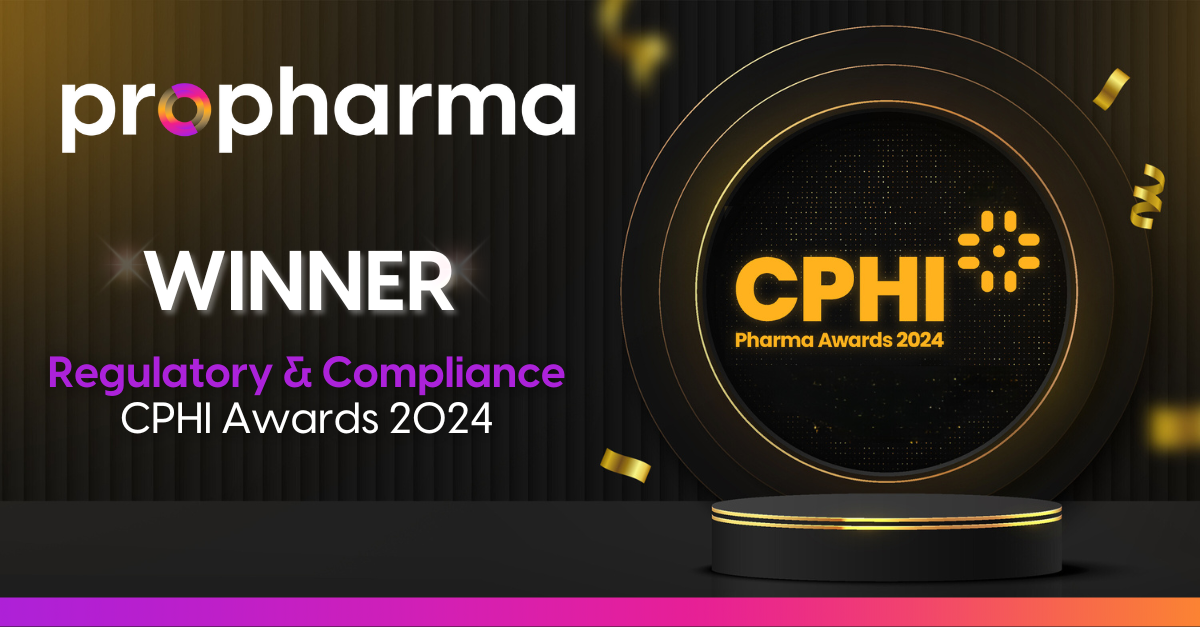
October 9, 2024
ProPharma Receives 2024 CPHI Regulatory and Compliance Award
ProPharma wins CPHI Pharma Award for excellence in regulatory and compliance innovation, enhancing efficiency and accelerating market access for life-saving therapies.
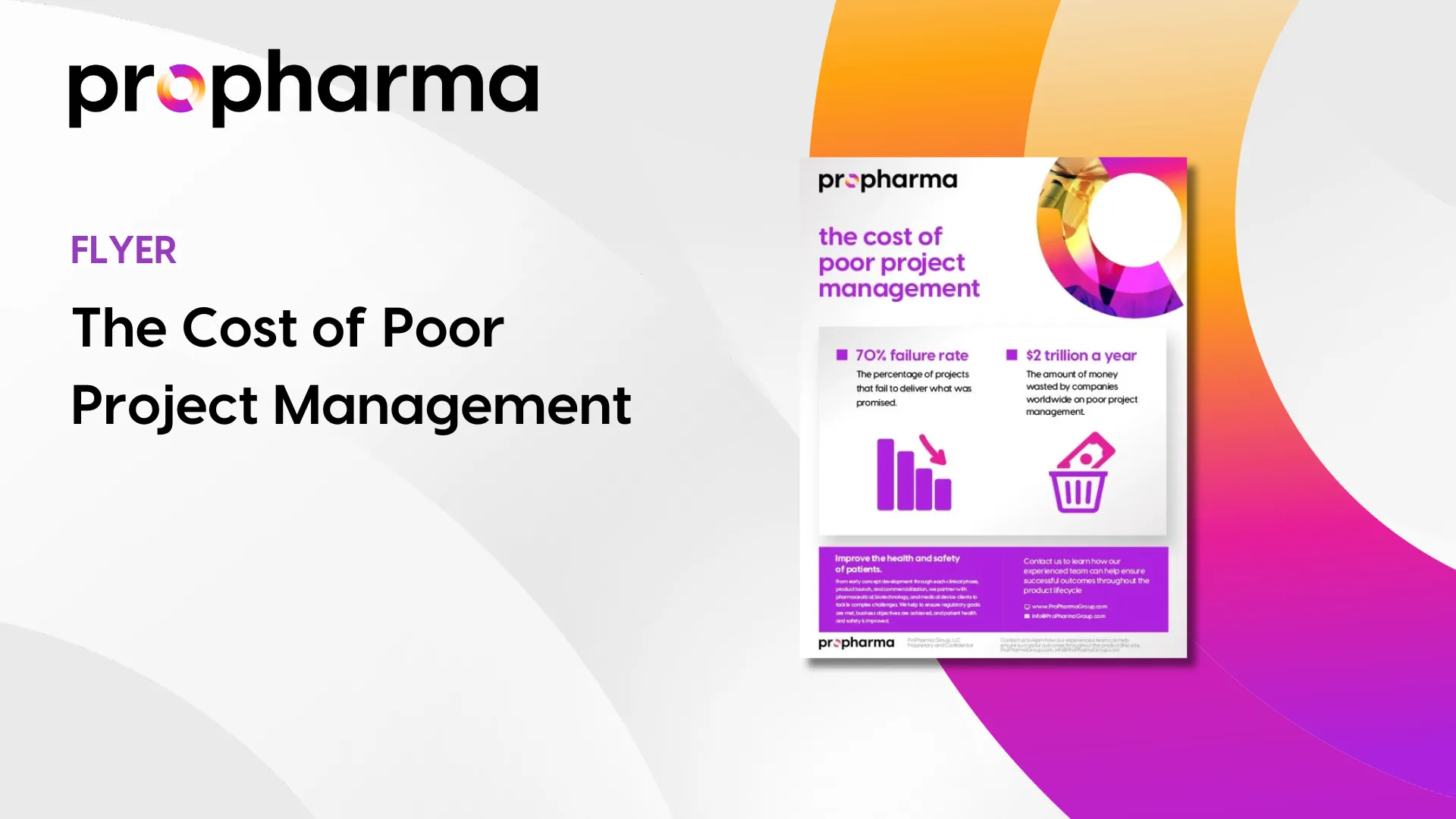
June 10, 2022
The Cost of Poor Project Management
Project Management isn’t for the faint of heart. There is a shockingly high rate of project failure… but on the other hand, great project management can be a key differentiator that leads a company...
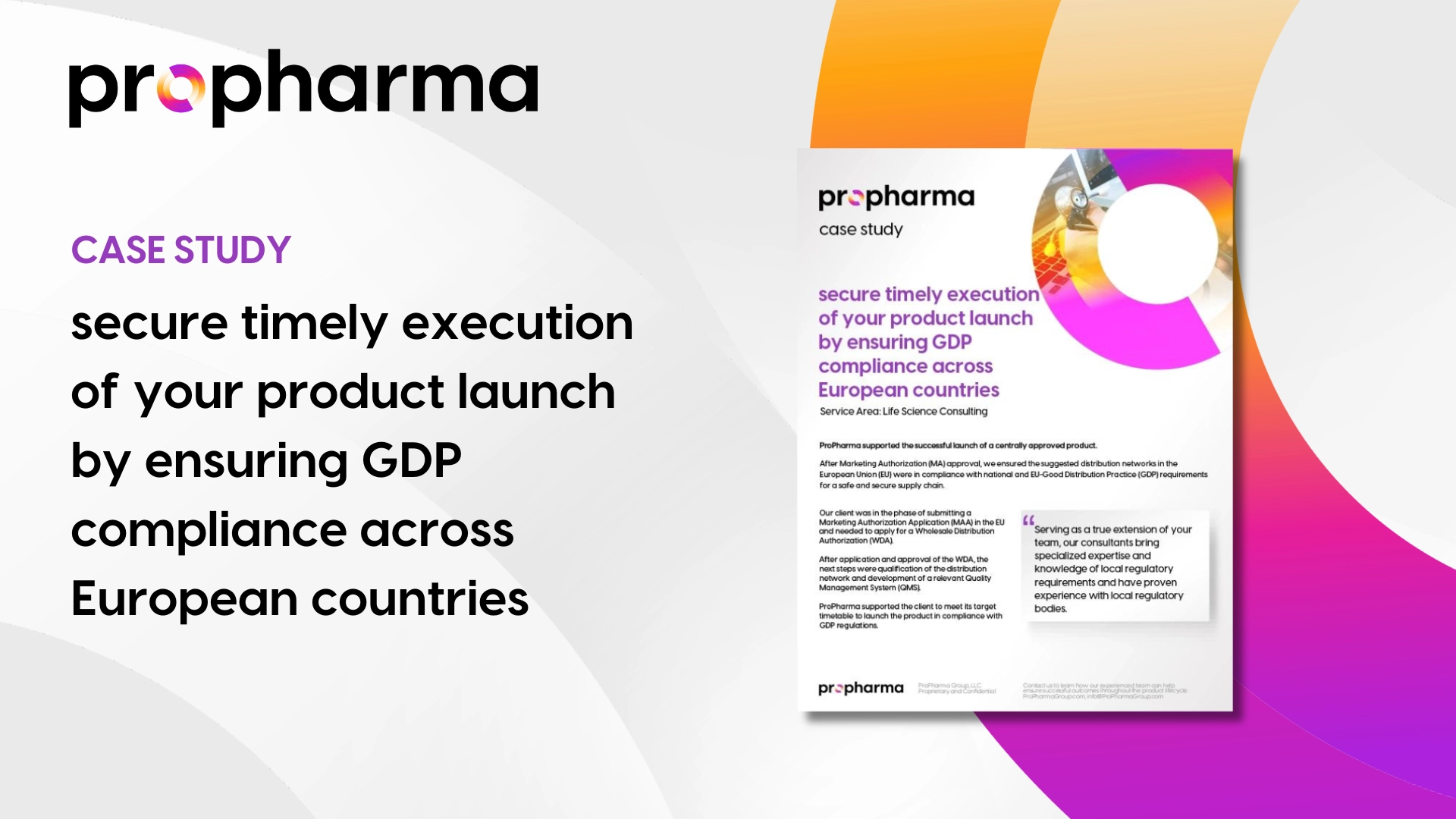
August 31, 2022
Successfully Passing MHRA Inspections for Overseas Manufacturing Sites
ProPharma offers GMP and GDP compliance services from clinical development to commercial distribution of the products' lifecycle. ProPharma’s Compliance and Quality team completed the first on-site...
News & Insights
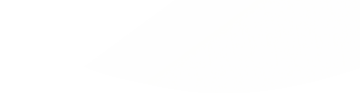
Complex Needs Require Custom Solutions
ProPharma builds solutions at the intersection of innovation and flexibility. We’re here to offer a custom alternative that fits your unique needs. Standout solutions scaled to your size.